Living sustainable is not just something we say, it is our company vision. We strive to be an industry leader in sustainability and reducing our overall carbon footprint by implementing a variety of energy saving programs, water recycling, and working with local governments and municipalities. Our sustainability goals don’t stop with just our facilities. We have been using recycled PET since the early 90’s with key retail partners. In 2011 we introduced our EcoStar® material that is made from post-consumer recycled PET. We purchase post-consumer recycled PET bottles and thermoforms from material recovery facilities (MRF’s) to help keep over 1 billion PET bottles from going to the landfills each year. By diverting these bottles from landfills, we are able to close the loop and create sustainable results.
Environmental Savings Calculator
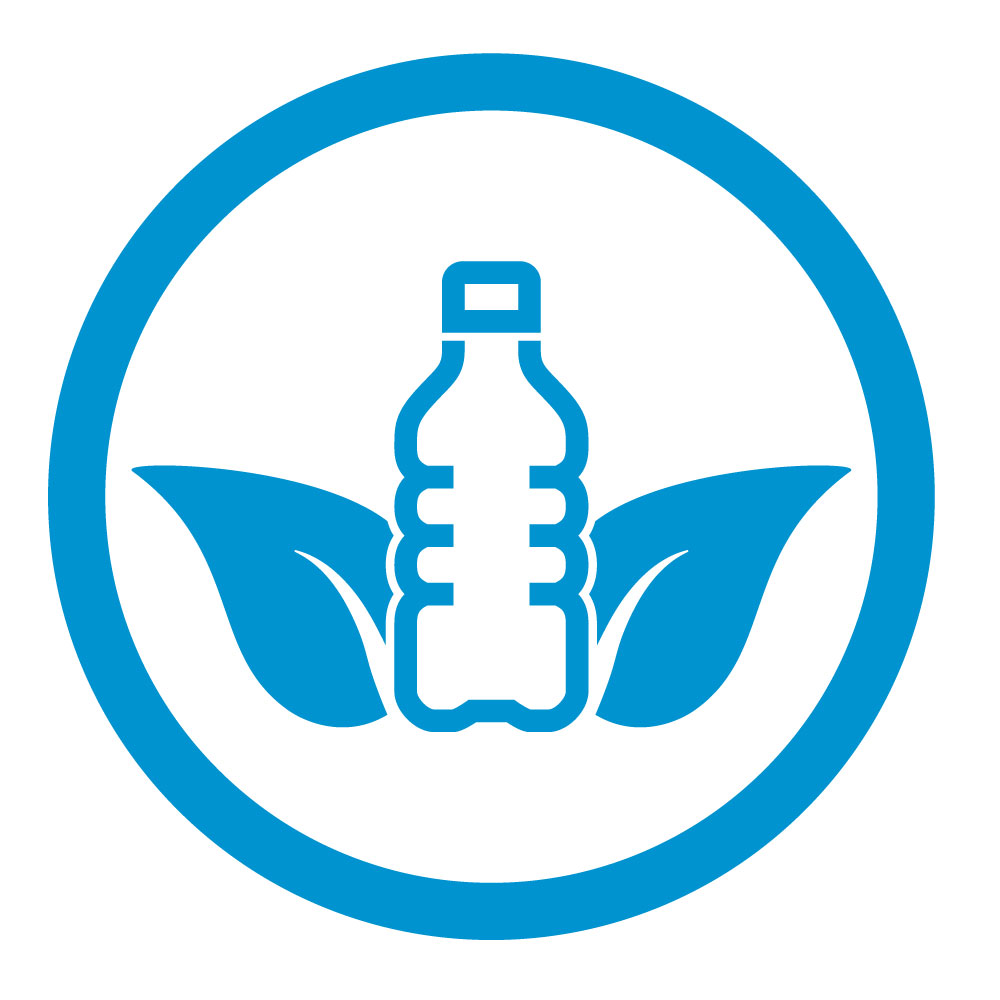
EcoStar®
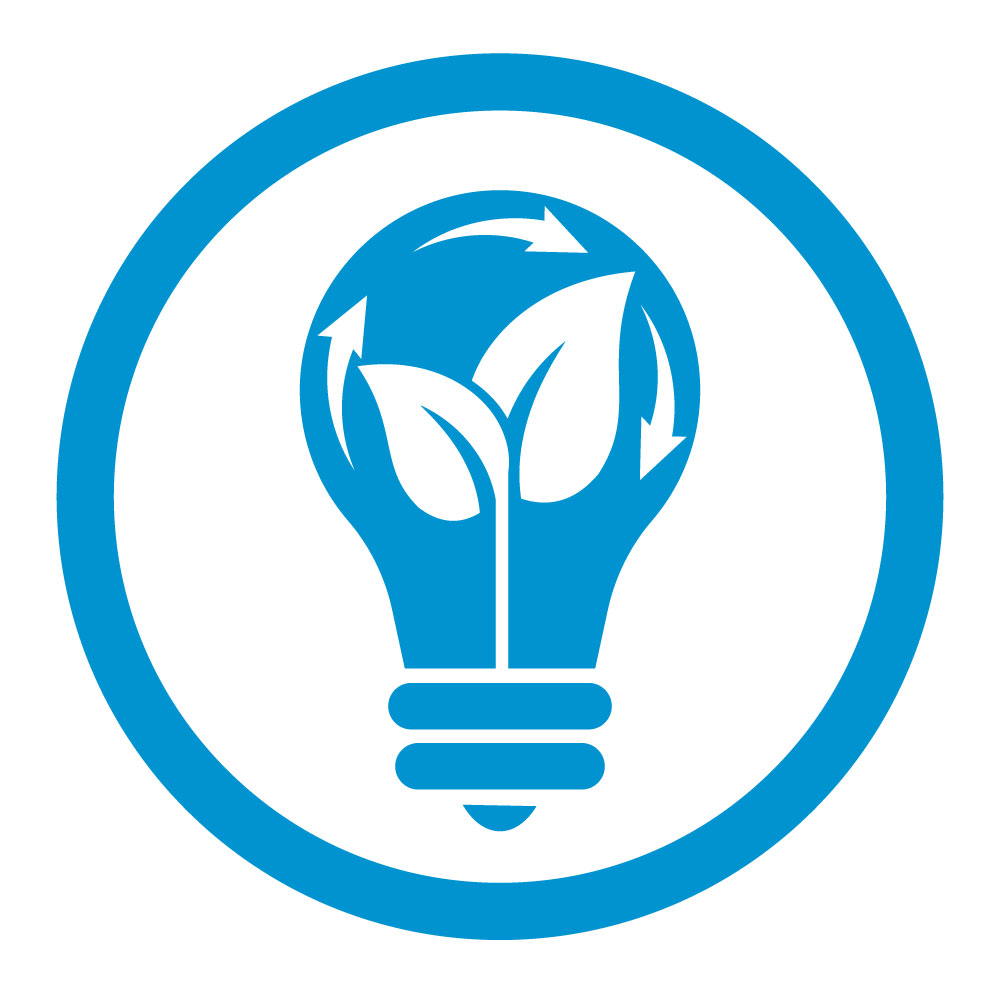
Energy Saving
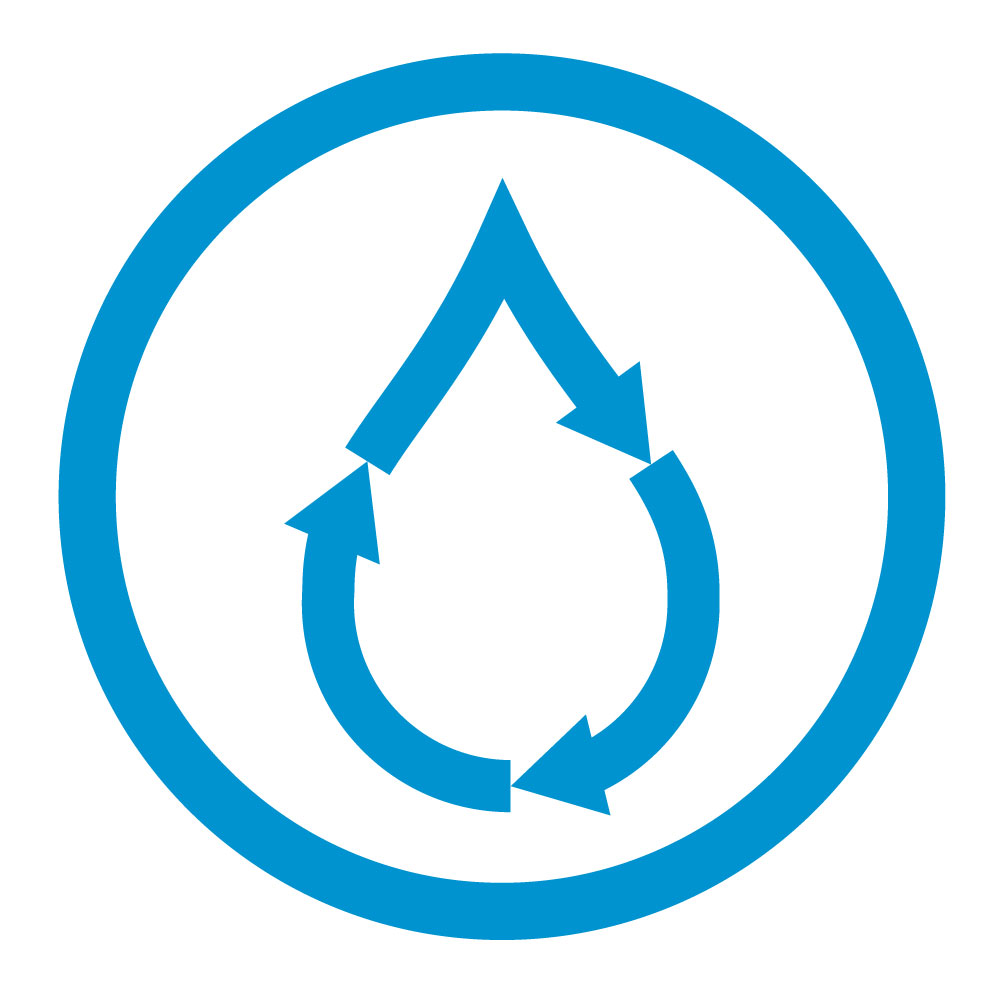
Water Recycling
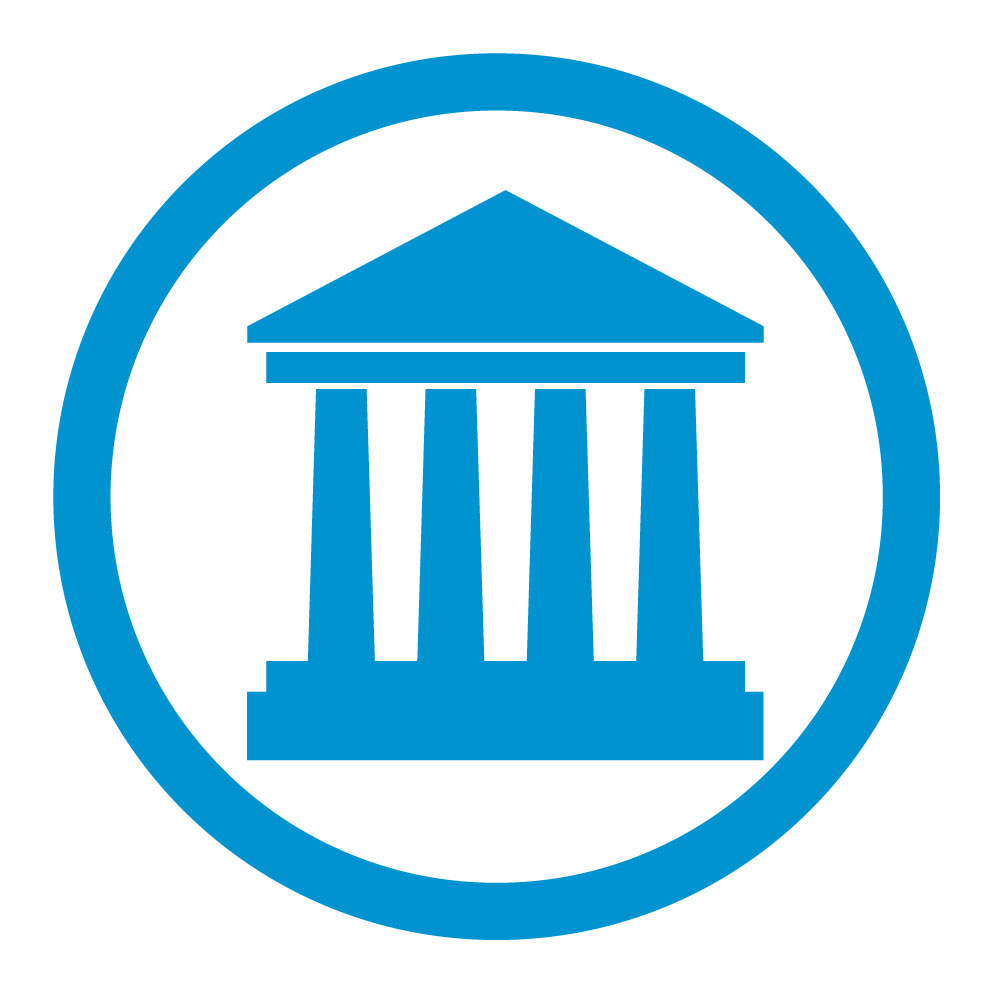
Government
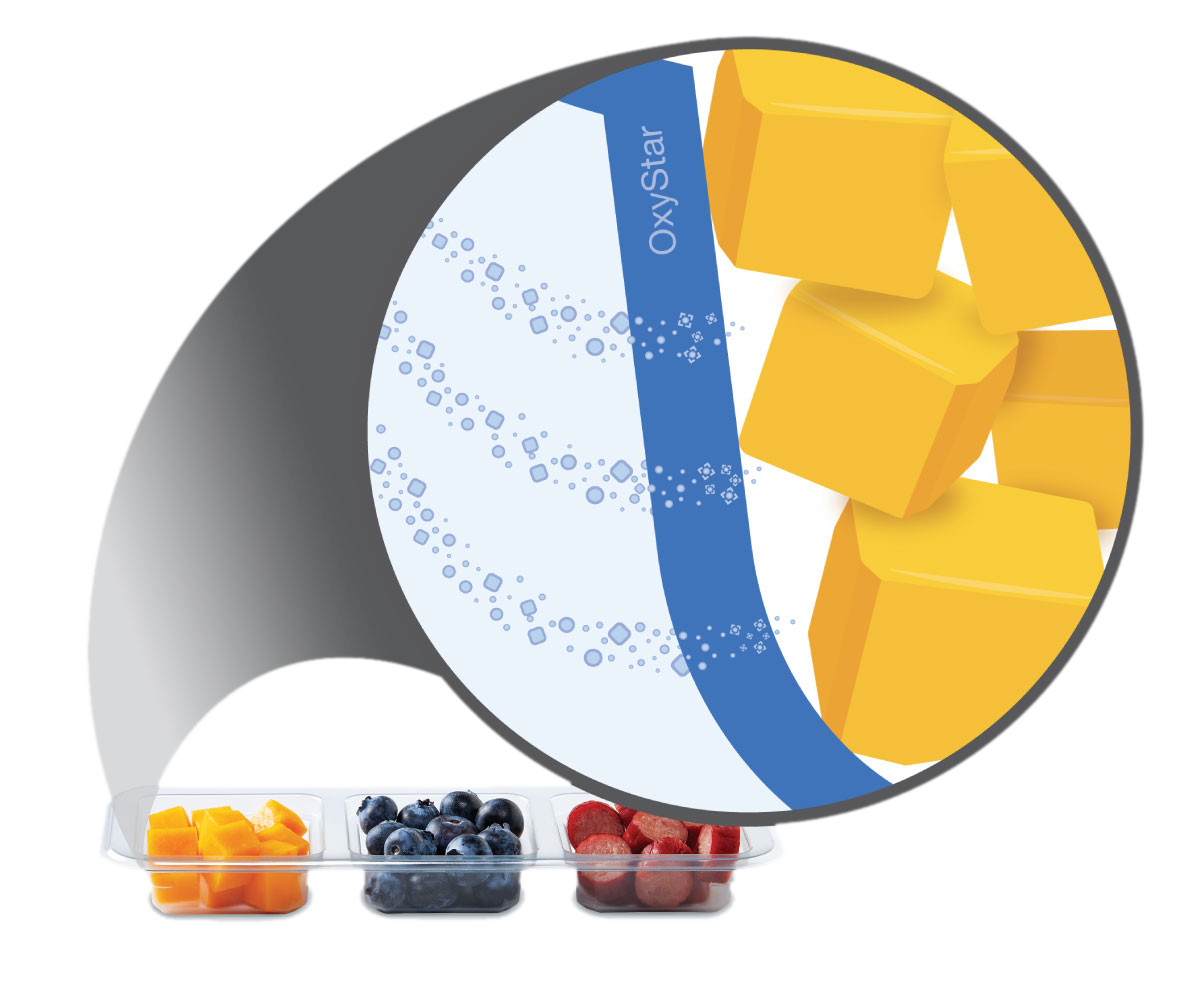
OxyStar®
When creating our custom food packaging, our number one challenge is figuring out how to make the product last longer. Direct oxygen contact with perishable foods has been a problem for food manufactures since the beginning of time, but not no more. Introducing the very first PET recyclable barrier material that can be designated with the #1 recyclable symbol, OxyStar®. OxyStar is an application that utilizes an oxygen scavenging agent to find and slow the oxygen to keep your product lasting longer. Most barrier solutions today are classified as a #7 recycle symbol that cannot be put back into the recycling stream, but not OxyStar.
Using PET with our OxyStar barrier material allows OxyStar to be classified as a #1 recycle symbol. This classification allows the packaging to be put back into the recycling stream to be used over again. OxyStar is FDA compliant for direct food contact to ensure your products meet all quality guidelines to keep your customers safe. Creating a package that gives your products a better way to keep your products fresher for longer, increases product shelf life while making a sustainable impact is how we make simply better packaging.
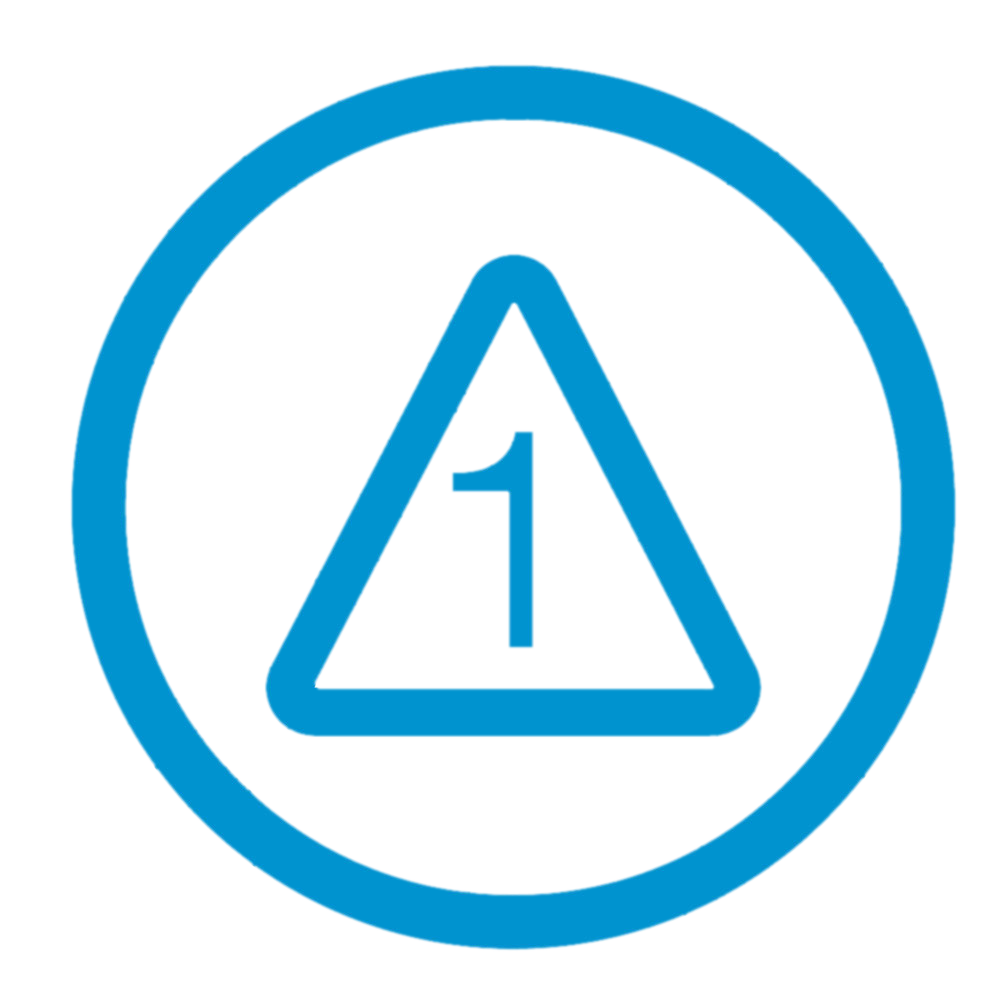
First #1 Recyclable Barrier Package
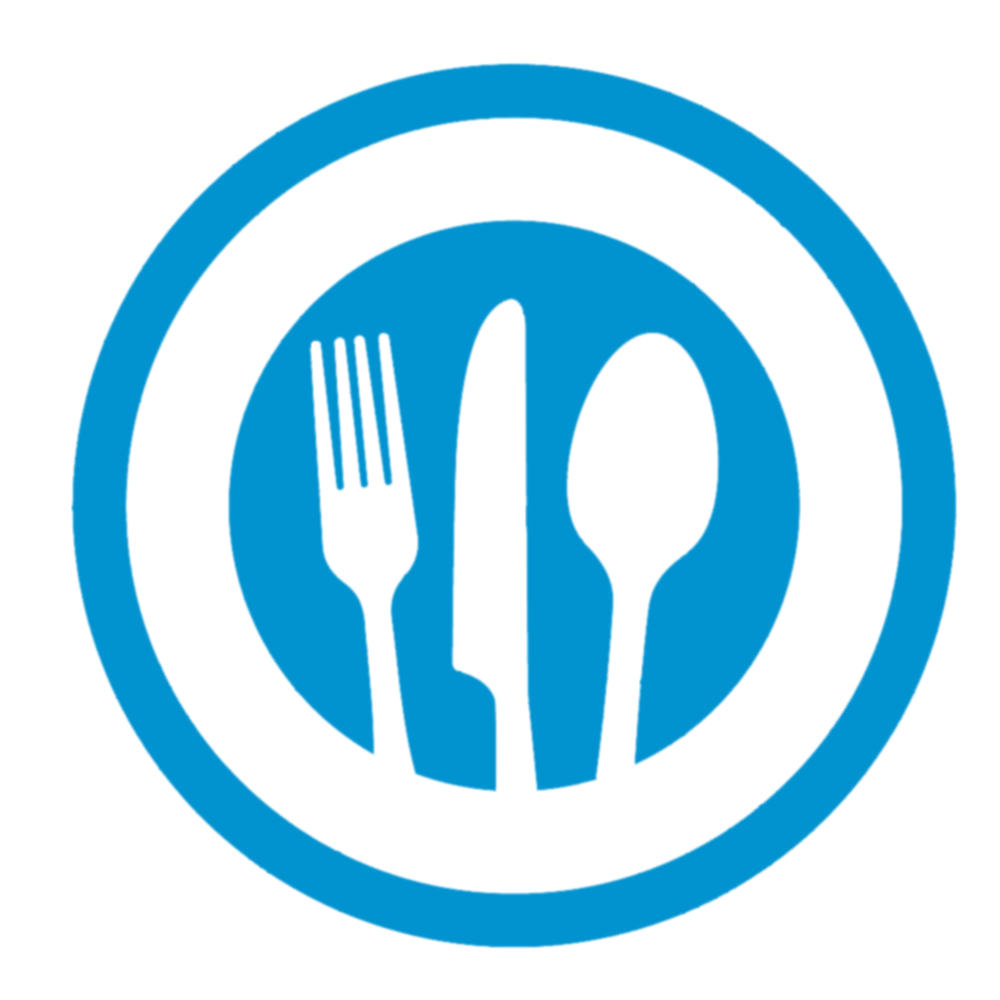
Increased Shelf Life
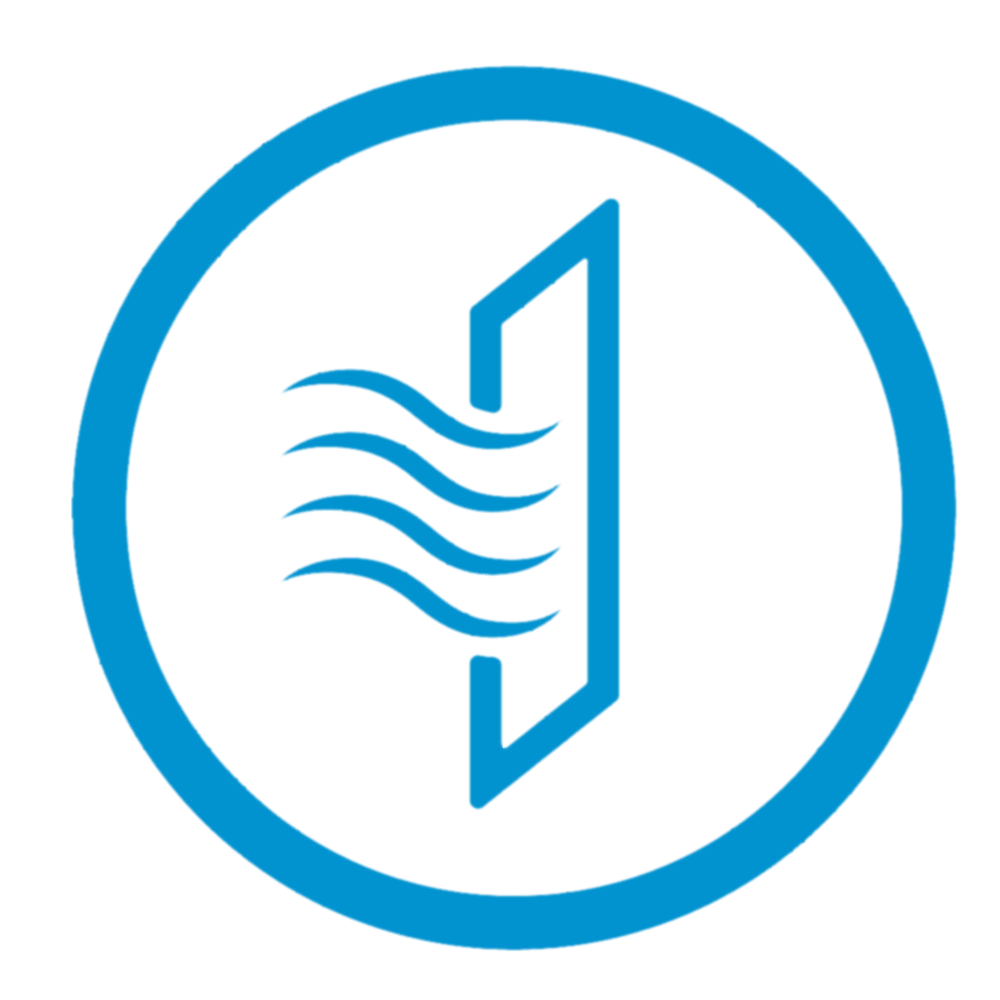
Barrier Packaging Helps Block Oxygen
OxyStar is combined with our PET material using a patent pending extrusion process. As a result of our patent-pending process, we have created a PET material that incorporates an oxygen-scavenging agent in the food contact layer. PET has a naturally low OTR (oxygen transmission rate), and this construction slows down the flow of oxygen molecules through the package from the outside. Once the scavenger agent finds an oxygen molecule, it attaches to it and binds the oxygen within the sidewall of the thermoformed package. This process helps keep oxygen away from the contained food products to ensure they stay fresh for a longer period.
OxyStar is going to disrupt the barrier packaging market. As the first barrier material with a #1 resin identification symbol, it is a way to keep your products safe from oxygen ingress and can be recycled and used again. OxyStar works well with products requiring a high oxygen barrier such as meats, cheeses, nuts and cut fruits with high vitamin C content. All thermoformed packaging that uses our OxyStar material are compatible with PET recycling and reuse processes to help support your sustainability goals.

Our EcoStar material is something we are very proud to talk about. We are at the cutting edge of environmentally conscious packaging materials with our EcoStar material. EcoStar is a food grade post-consumer recycled PET material that is made from curbside-collected bottles and thermoforms and is 100% recyclable. Commitment to recycling PET by reclaiming plastic bottles and thermoforms and turning them back into consumer packaging is how we at Placon make simply, better packaging. Reuse, recycle and replastic is our vision to get the most out of plastic.
We are proud to say that we complete a closed loop process when creating our EcoStar packaging. Simply look for the #1 inside the recycling symbol to determine if the item is PET or not. All PET bottles and thermoforms can be used in our process, which are used to make our EcoStar post-consumer recycled PET plastic sheet.
Step 1:
PET flake is extruded into our EcoStar plastic sheet, used for food, medical and retail packaging.
Step 2:
Packaging made using our EcoStar material is then shipped to distributors and customers across the United States to be used for food, medical and retail products.
Step 3:
Consumers use food, medical and retail products every day. Once they are done using them, they can simply toss the EcoStar packaging into their recycling bin.
Step 4:
Recycling bins filled with EcoStar and other PET plastic are placed curbside to be collected by local recycling companies.
Step 5:
Local recycling companies then process the curbside collected PET plastic and is made into post-consumer PET bales. These bales are then sent to Placon in Madison, WI to be made into EcoStar post-consumer PET packaging.
Step 6:
Once the post-consumer PET bales arrive at Placon, they are cleaned, sorted and made into clean PET flake.
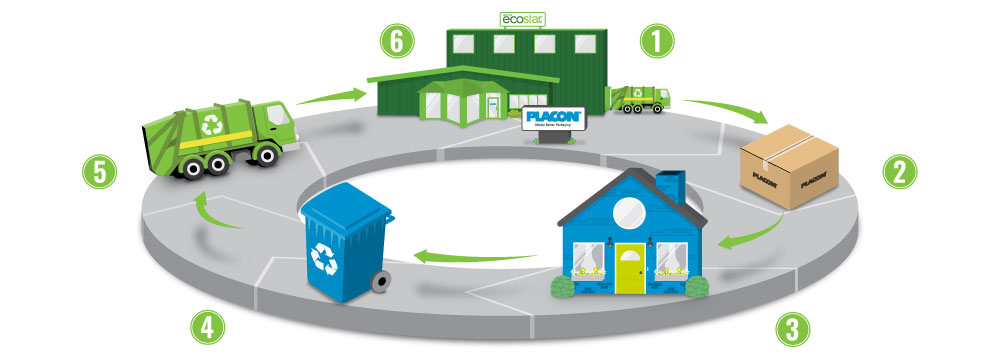
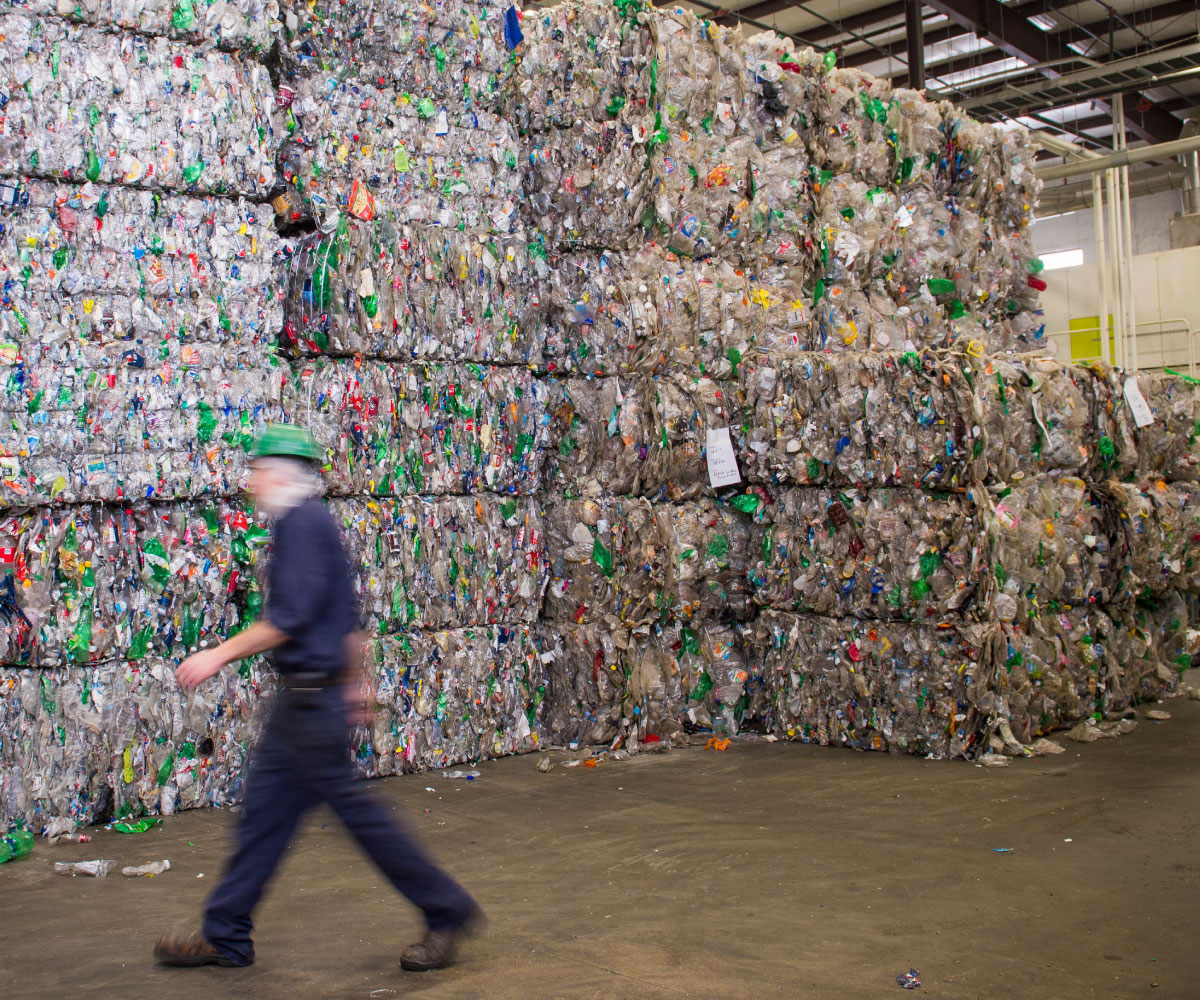
We opened our Madison, Wisconsin recycling facility 2011, with the vision to promote a sustainability message and create sustainable packaging solutions in the food, retail and medical market space. When operating at full capacity, our facility recycles 83 lbs. of inbound PET bottles and thermoforms per minute. That is equal to diverting over 120,000 lbs. of PET containers from landfills each day. Per year, this would add up to over 4 billion containers recycled – enough PET water bottles to wrap around the earth 16 TIMES. Each ton of plastic recycled means saving 3.8 barrels of oil, which would mean conserving more than 75,000 barrels per year based on the amount of PET we could recycle and remake into usable thermoformed packaging.
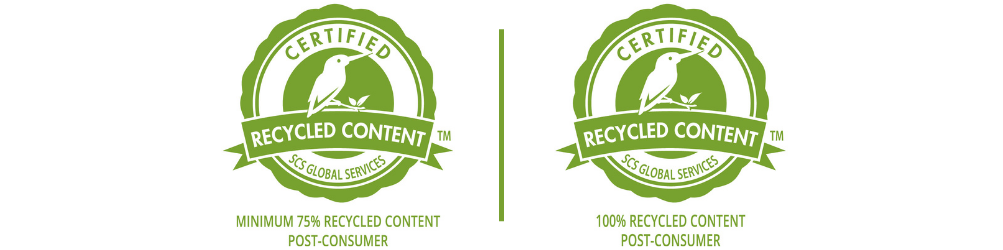
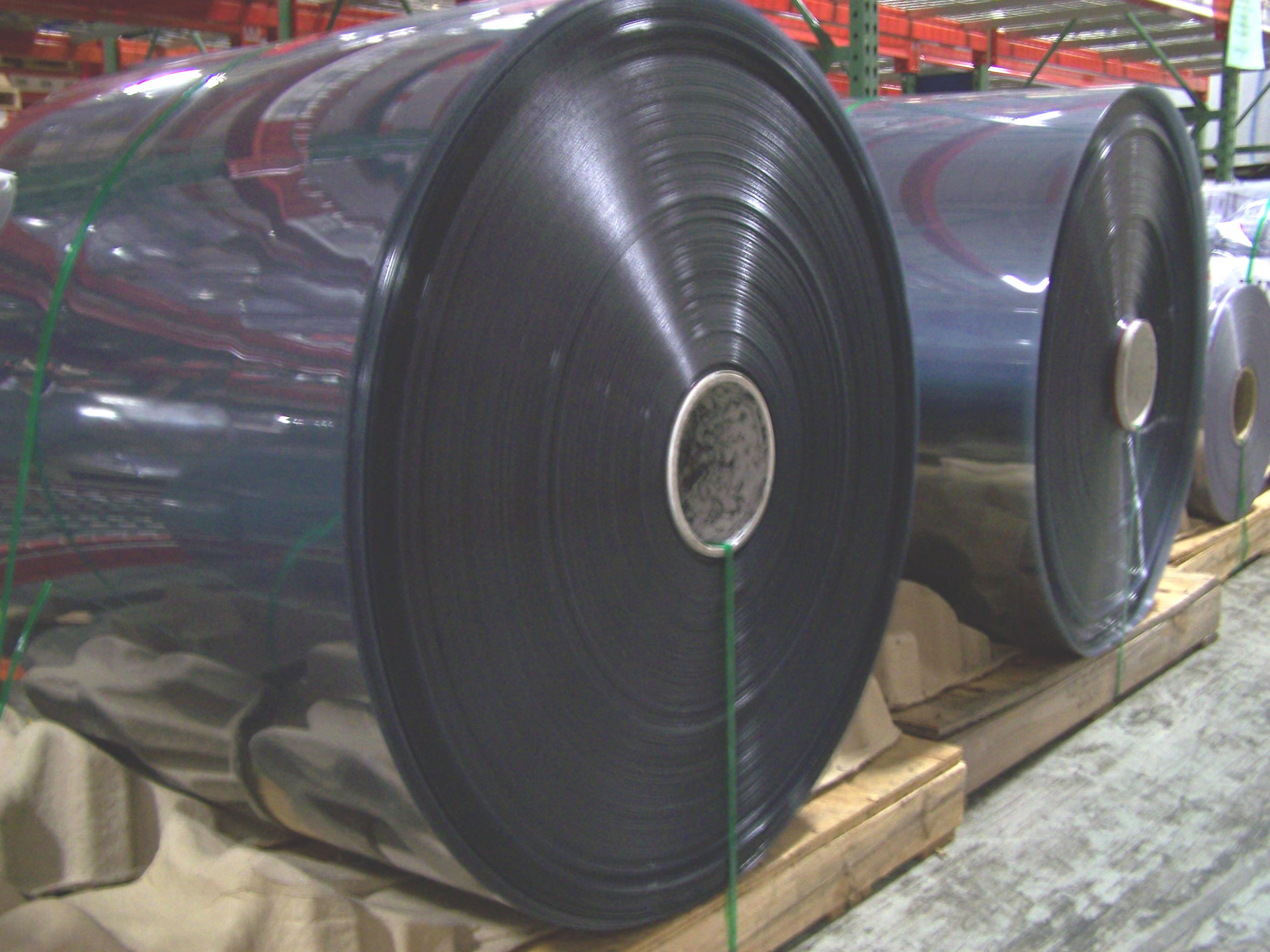
CERTIFIED SUSTAINABLEAs a leader in sustainable packaging, we want you to know the sustainability impact you are making by using our packaging. Our RPET-F75 and RPET-F100 PET material are certified by SCS Global Services as having post-consumer recycled content. For any product that is made using 75% or 100% post-consumer recycled PET you will see the SCS Global Services logo to signify this claim.
SCS Global Services (SCS) has been providing global leadership in third-party quality, environmental and sustainability verification, certification, auditing, testing, and standards development for three decades. Its programs span a cross-section of industries, recognizing achievements in green building, product manufacturing, food and agriculture, forestry, power generation retail, and more. SCS is accredited to provide services under a wide range of nationally and internationally recognized certification programs. Consistent with its mission, SCS is a chartered benefit corporation, reflecting its commitment to socially and environmentally responsible business practices.
|
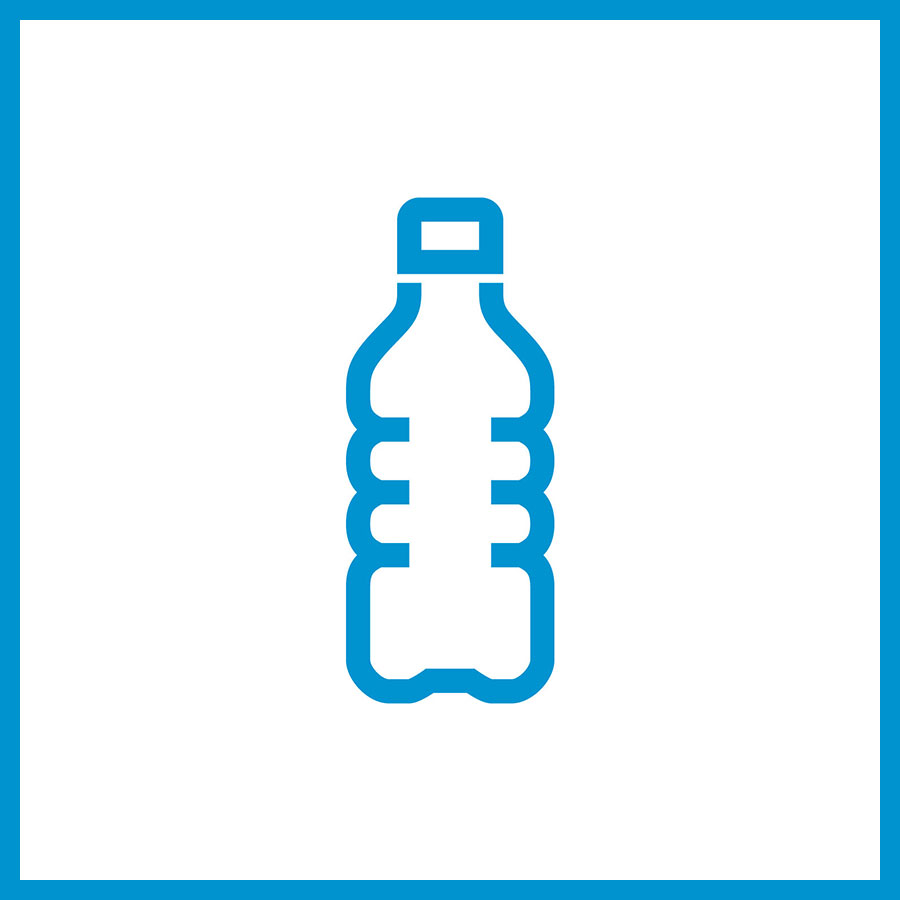
Throughout our website, you will see on our stock food and retail pages, a line item in the product specification section that indicates bottles per unit and bottles per case. The listed value represents the quantity of plastic bottles and thermoforms that are being redirected from landfills to make that product. We have taken the average weight of one standard water bottle (9.9 grams) to emphasize the sustainable impact you are making with your packaging choice and providing you with information to share with your customers.
Creating sustainable impact comes down to individuals, businesses and local community members choosing to make the environment their priority. At Placon, we encourage everyone to choose to recycle. By knowing more about the different types of plastics, you can understand how your packaging choice makes a difference. A few things you can do include:
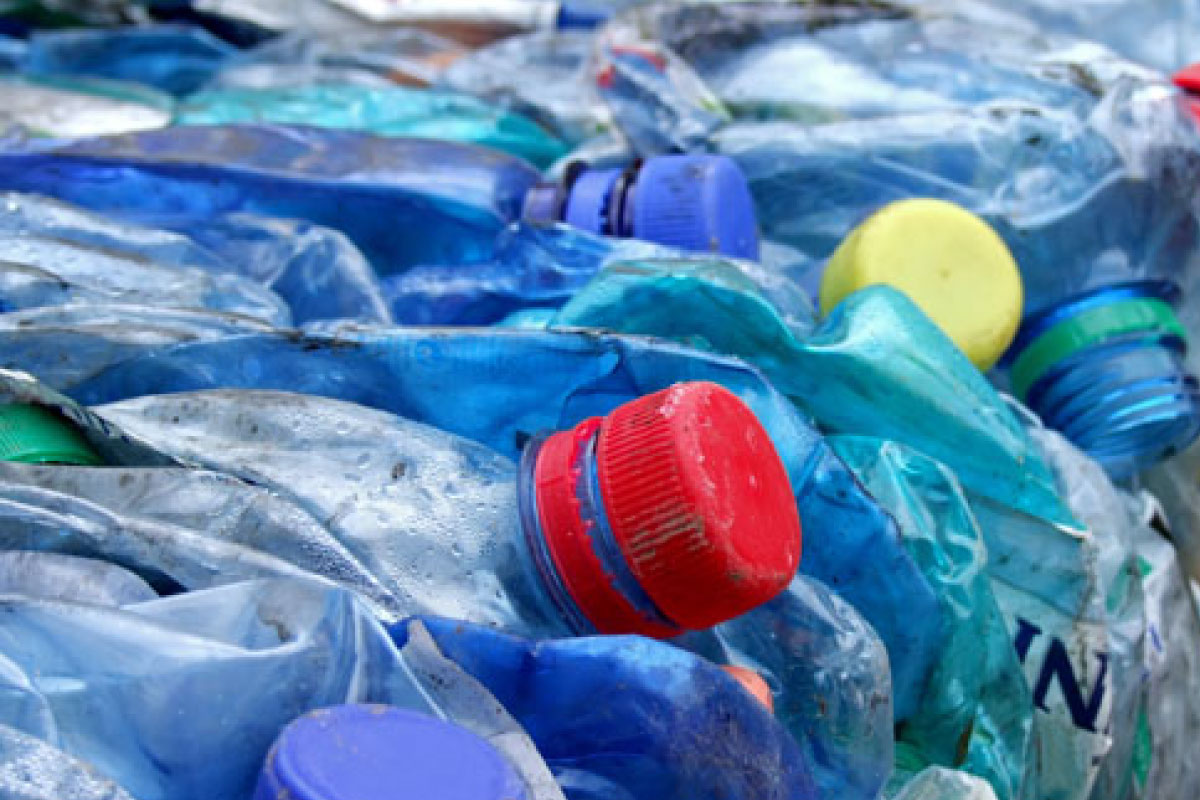
PET is the most widely recycled plastic type and accepted globally. Spread the word and help us close the loop by ensuring PET products return to the recycling stream where they can be repurposed into new products.
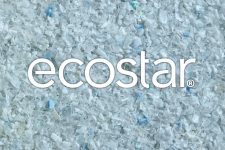
When shopping, look for our EcoStar logo that can be found on food and retail packaging across North America. This logo embodies our commitment to keeping PET out of landfills and encourages all consumers to recycle.
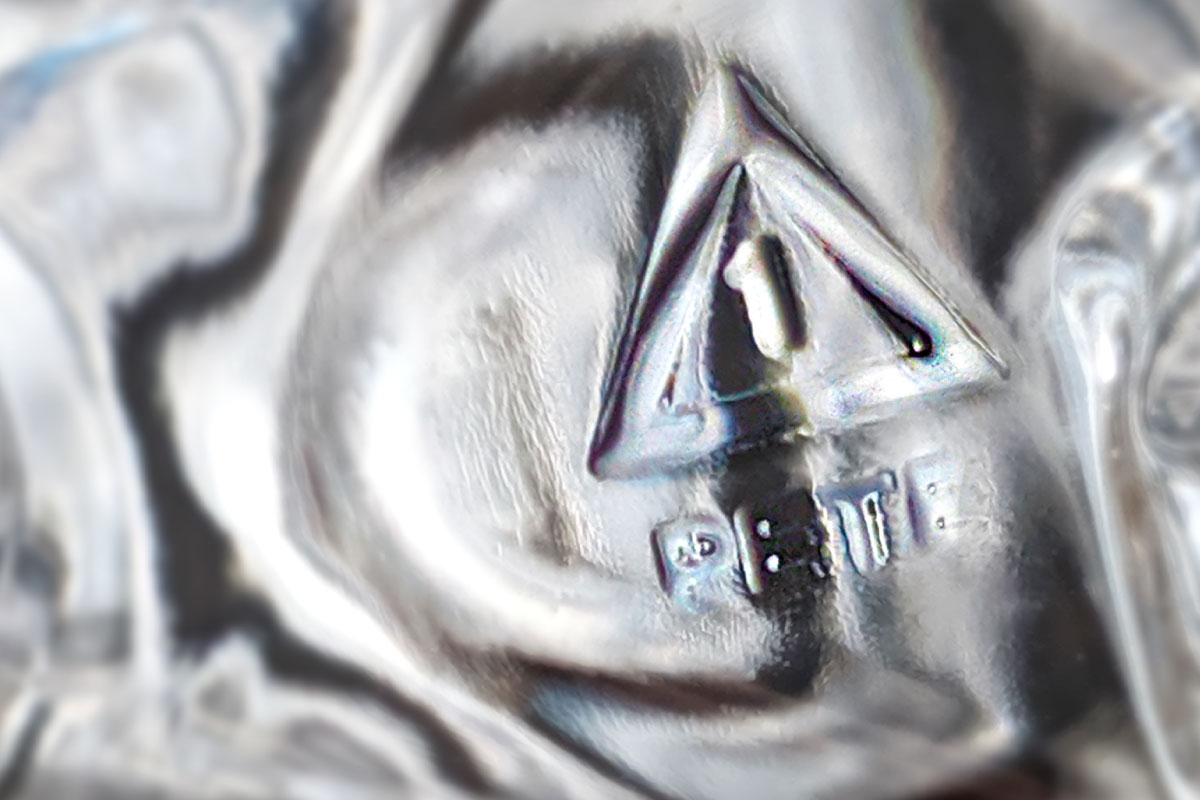
Look for the #1 identification code. The #1 recycling symbol indicates that the container is made of PET, which is the most globally recycled plastic today. PET can easily be recycled by discarding it in a recycling receptacle.
PET is an acronym for Polyethylene Terephthalate and is best known as the clear plastic used for water and soda bottles. Globally recognized as a safe lightweight and flexible material, PET is also 100% recyclable. In fact, PET is the most widely recycled plastic in the world, with recycling rates increasing each year. If you are not sure which plastics are made from PET, all you have to do is look at the resin identification code on the bottom of the container. If it is made of PET, you will see a symbol featuring the number “1”, surrounded by the three chasing arrows that indicate recyclability.
Both virgin and recycled PET are used to package a wide range of products. These products range from beverages, food, cosmetics and toys. PET is also a common component found in fiber or fabric applications such as, carpeting, clothing and sleeping bags where it is commonly referred to as “polyester”. PET is used worldwide, therefore it has a high value and is particularly important to recycle. By taking purchased curbside collected bales of PET bottles and thermoforms, we are able to keep this material out of landfills, so it can be used in making new packaging for consumers to use and enjoy.
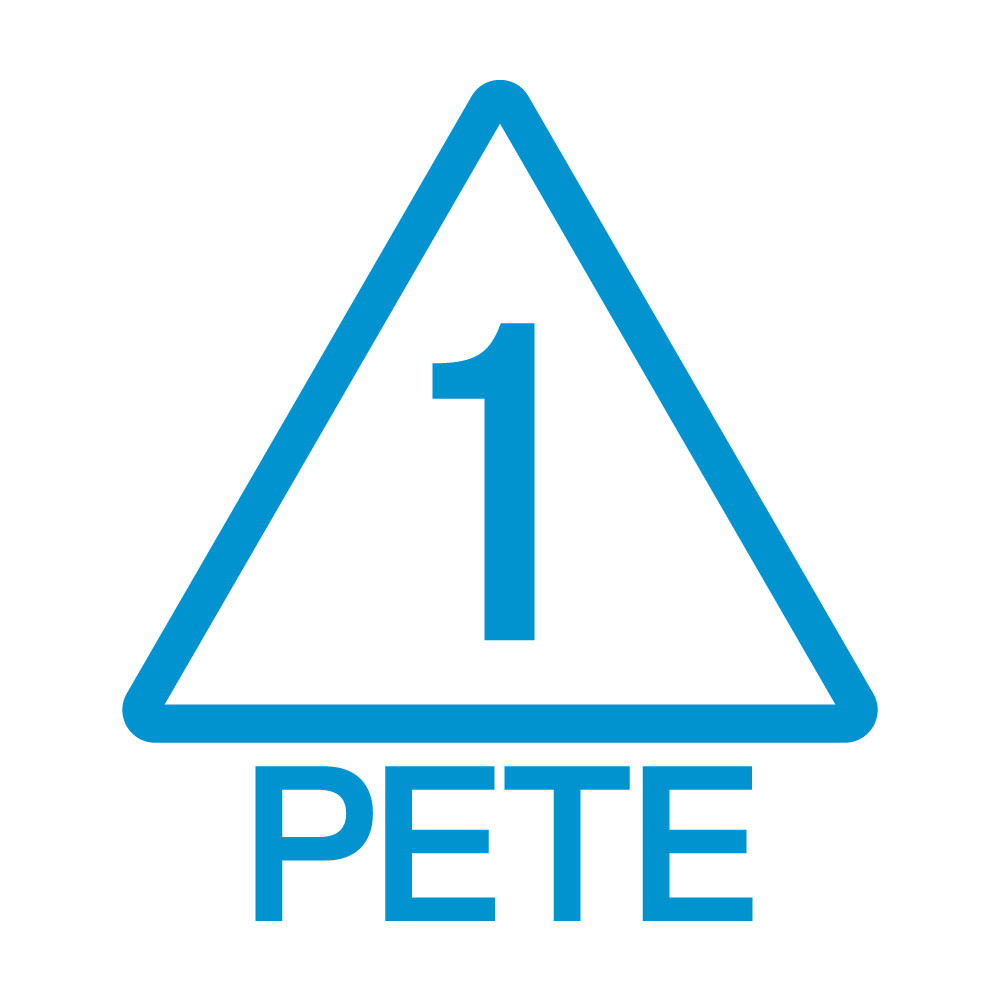
Description
Properties
Product Applications
|
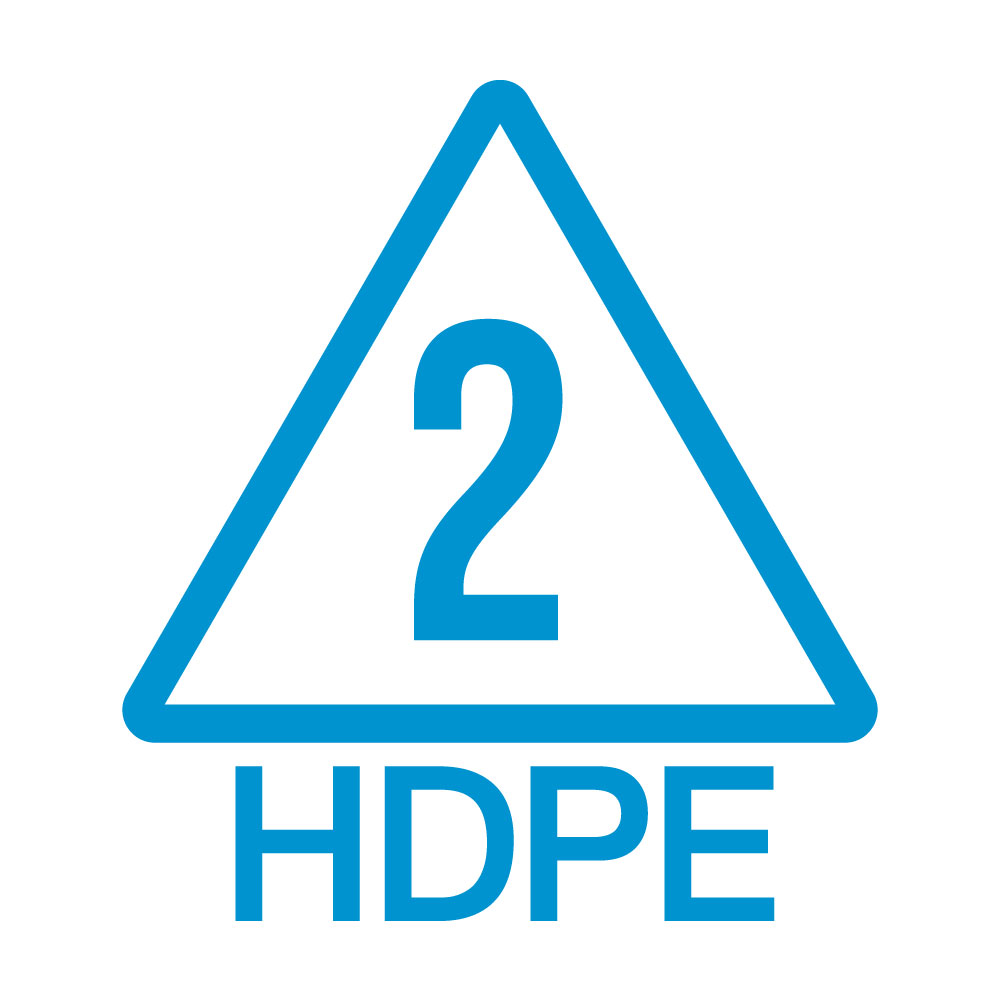
Description
Properties
Product Applications
|
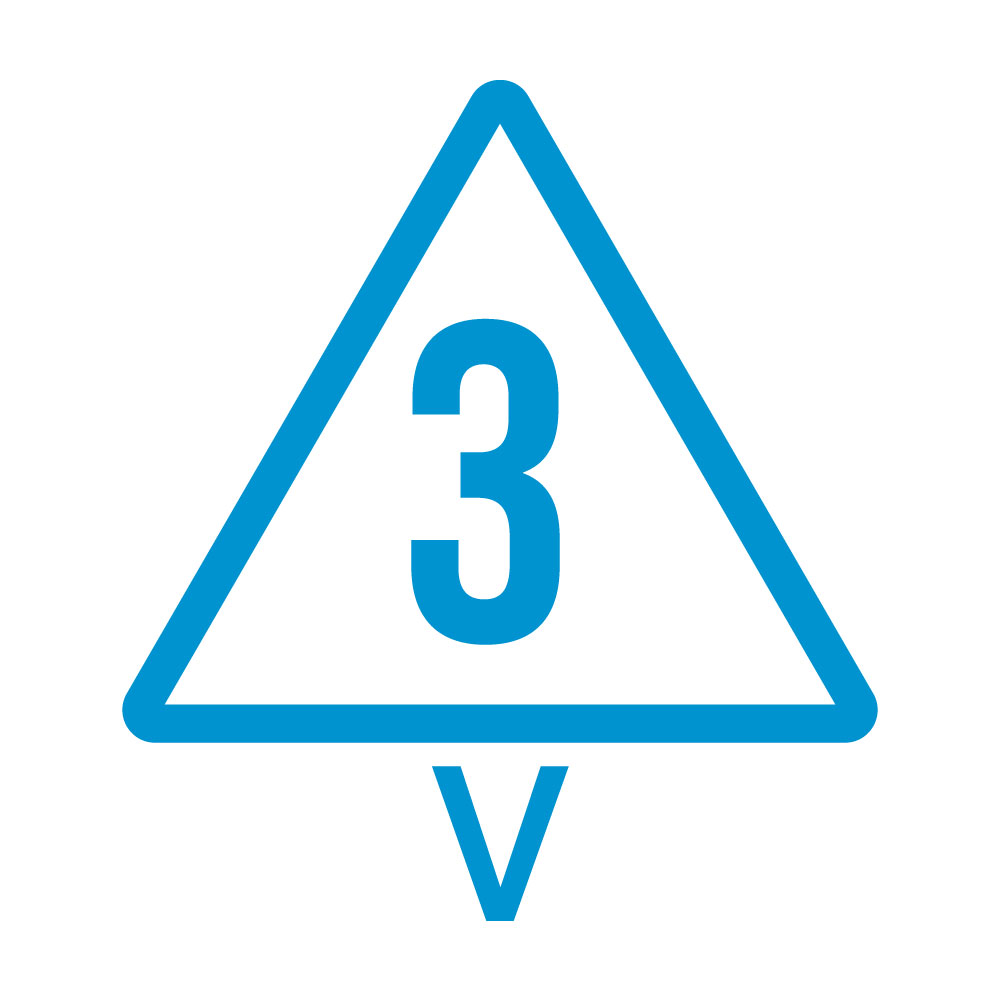
Description
Properties
Product Applications
|
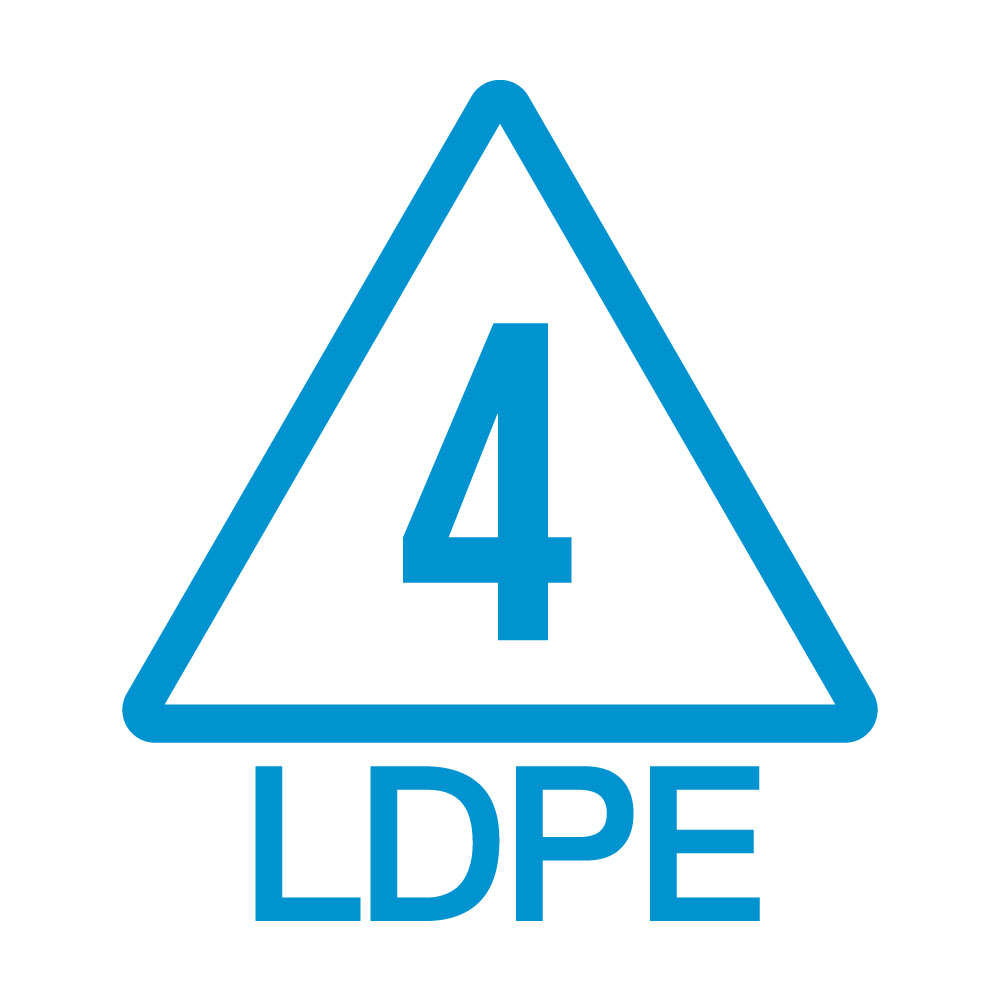
Description
Properties
Product Applications
|
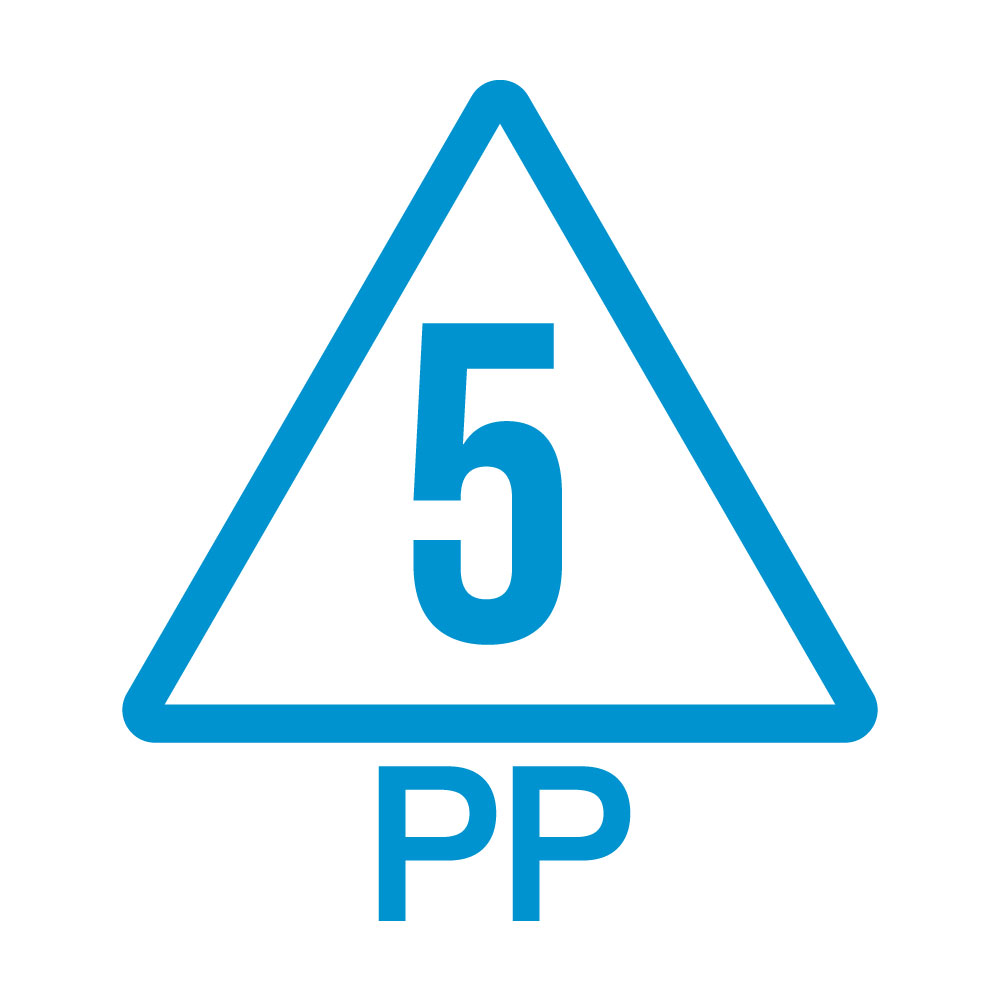
Description
Properties
Product Applications
|
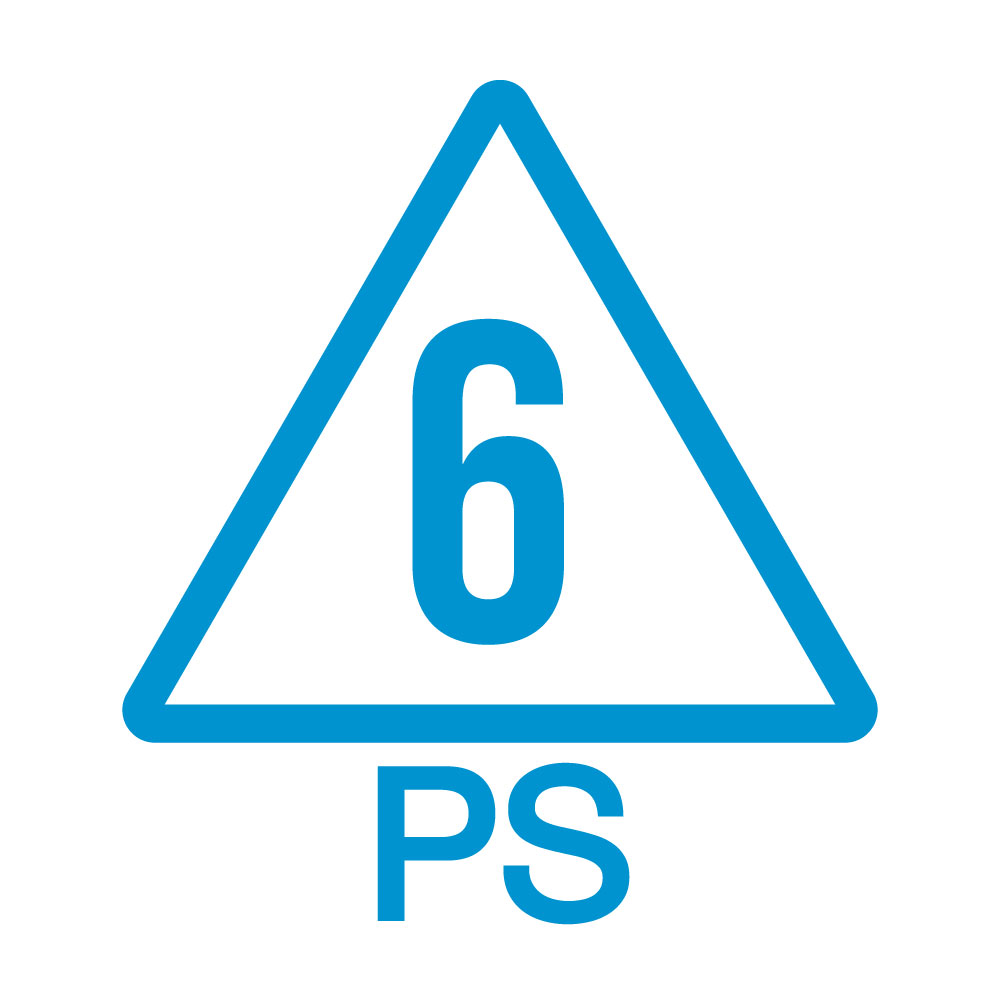
Description
Properties
Product Applications
|
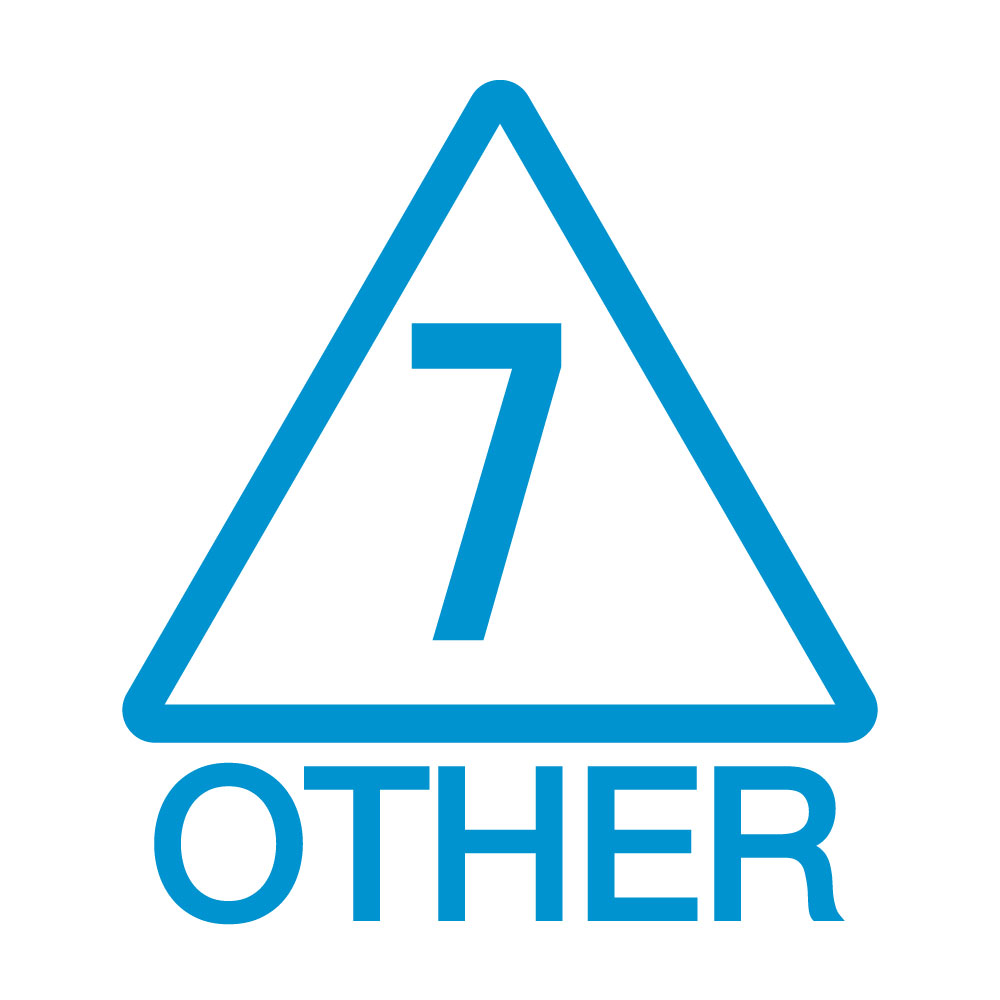
Description
Properties
Product Applications
|
Recycling may not be available in all areas. Check to see if plastics recycling is available in your community.
Source: https://plastics.americanchemistry.com/Plastic-Resin-Codes-PDF/